Nazca Neo Linka 導入事例 CASE05
直径1mm以下の歯科用針も加工、
すごい町工場が抱えていたNCプログラム送受信の問題
丸物の精密加工を手がける、有限会社コスズ製作所(以下、コスズ製作所)は、φ20(直径20mm)をメインに、φ1以下の小径加工にも対応。医療関連や半導体関連の部品、コネクタ部品など、1個から10,000個までの多様なニーズに応えています。
20台近くの工作機械を駆使することで、さまざまな形状や表面の加工を実現しています。また、材質も、鉄、アルミ、真ちゅうをはじめ、難削ステンレスからNi合金まで、難削材も扱っていることが特徴です。
丸物加工の頼れる加工先であるコスズ製作所ですが、実はある大きな悩みを抱えていました。この道20年の技能者である鈴木信さまは、次のように語ります。
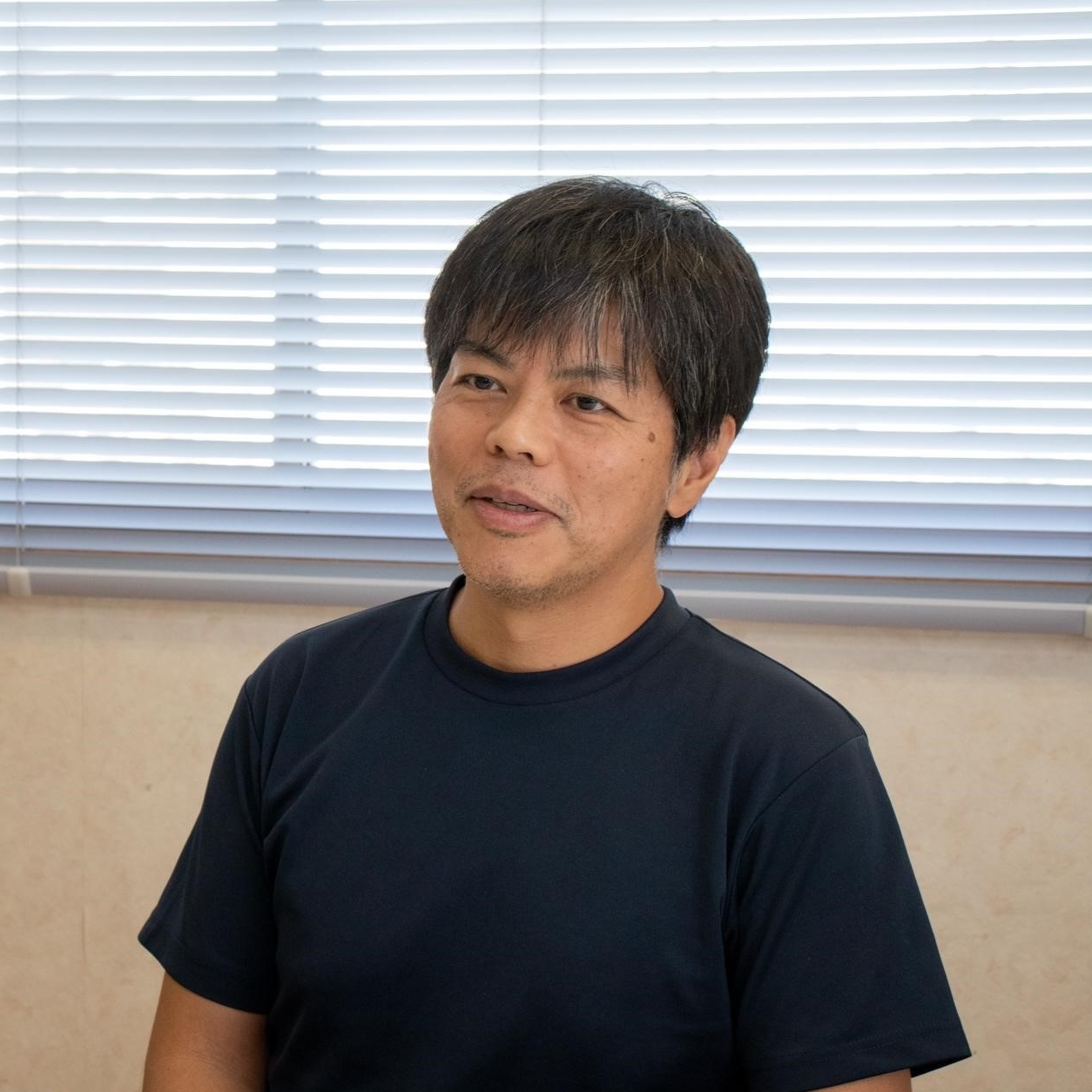
営業技術 鈴木 信 氏
「15年以上、NCプログラムの送受信に『RS232C』という旧来の通信方式を使っていました。パソコンが老朽化していたこともあって、送受信に10~15分のロスが出てしまうのです。データが重いとエラーになり、送受信の失敗も頻発していました。
また、NCプログラムを送受信するために、現場と事務所の往復が必要でした。設計用のパソコンで加工データを作り、プログラム送信用のパソコンに転送。その後、プログラム送信用のパソコンを現場に持っていき、RS232Cの端子から機械にNCプログラムを送る、といった具合です。
機械の画面上でもNCプログラムを微調整するので、加工が終わったら編集したNCプログラムをまたプログラム送信用のパソコンに送って、保存して……。
現場は、私を含めた専任の技能者2名体制です。プログラム送受信のロスがあるだけで全体の生産性に影響が出ていました。」と鈴木さま。
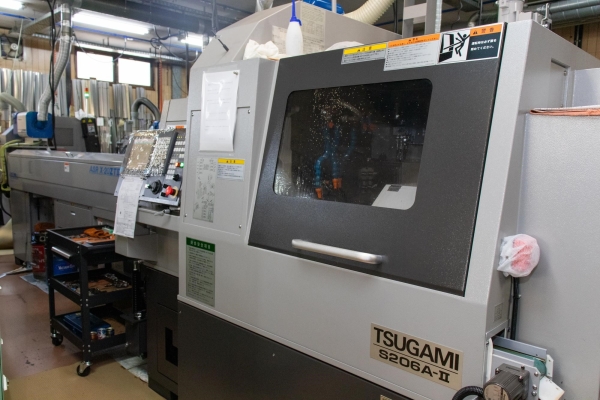
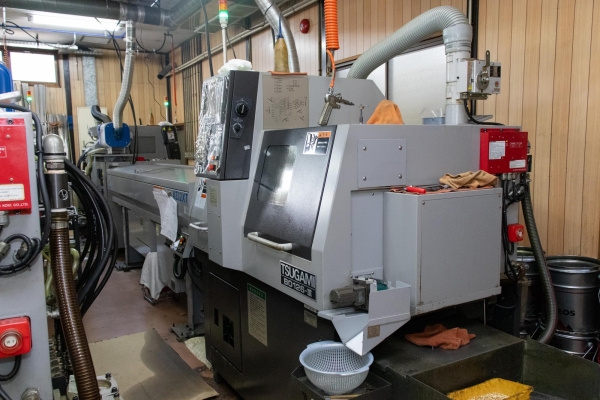
材料の投下から完成まで一気通貫で行う先端の工作機械を駆使。一人の技術者が設計と製作を兼ねることで、高品質を実現している。
また、夜間や土日祝日も機械を稼働させるなかで、機械停止が起きた際に気付ける仕組みがなかったことも課題でした。
鈴木さまによると、「とくに週明けまでに加工を終わらせなければいけない注文の加工時は、機械が稼働しているか心配になり、休日に社長が様子を見に来ていました。」とのこと。
さらに、日々異なる部品を生産しているため、機械ごとに生産性のバラツキがあることも課題でした。今後のために、生産状況を把握する手段を取り入れ、生産を標準化し、原価計算に活用したいという考えがありました。
以上の課題から、工場の稼働状況を把握するためのIoTシステムと、新たなNCプログラムの送受信ソフトが検討されました。
工場の稼働状況の見える化へ!
現場の意見に耳を傾けてくれたことが
新明和ソフトテクノロジを選んだ決め手
IoTシステムの導入を検討していた社長に、新明和ソフトテクノロジまで問い合わせいただき、ソリューション部 営業2グループの山本優斗(以下、山本)が現地を訪問しました。稼働監視は、IoTによる工場の見える化システム「Nazca Neo Linka(ナスカ・ネオ・リンカ、以下:Linka)」で難なくクリアできることに。NCプログラムの送受信の手間も「NAZCA5 DNC(ナスカファイブ・ディーエヌシー、以下:DNC)」の導入でほぼゼロにできると予測できました。
ただし現場には、システムが切り替わることへの心配の声も。そこで、山本から「まず実機を導入して、使用感をテストすること」を提案しました。
鈴木さまより、「このような山本さんの丁寧な対応が決め手となり、社長も導入を決めたようです。」と説明いただきました。
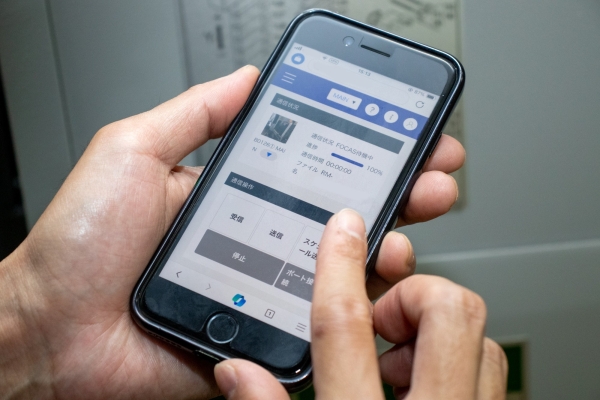
1回目のテストでは、タブレット版のDNCを使用。実際に使っていただくなかで「スマホ上で操作できた方がよい」という意見が出ました。鈴木さまは、当時の状況を次のように説明します。
「タブレットを操作してみると、両手がふさがって使いづらいと感じる部分がありました。ほかにDNC上でする操作といえば、NCプログラムの軽微な編集くらいです。
そこで思い切って『スマホ上のボタンを押す感覚で、操作できませんか?』と山本さんに相談しました。すると、山本さんも『やってみましょう』と前向きにお返事いただきました。」
鈴木さまの提案をもとに、スマホ用アプリを構築。これにより、スマホ上でNCプログラムの送受信が実現しました。さっそく2回目のテストを実施すると、「これは使いやすい!」という声をいただけました。
「もう段違いに操作しやすくなりました。アプリ上でNCプログラムと送信先の機械を選択して、送信ボタンを押せばすぐにデータが転送されます。ずいぶん便利になったな、と思いました。」と、鈴木さまからうれしい感想を聞けました。
15台の自動機すべてにLinkaを接続。
有線対応となったが、パトライトや電源装置につなげたLANケーブルは天井を這わせて1ヵ所にまとめ、配線もきれいに収まった。
IoTシステム導入で生産余力が生まれた!
自社ならではの技術に挑戦し、技術者としてのやりがいが向上
山本から操作方法をレクチャーさせていただき、現場での混乱もなくシステムを本格稼働できました。最近入社されたという技術職の方にも、「これなら使い勝手は心配ない」と安心いただいている様子です。
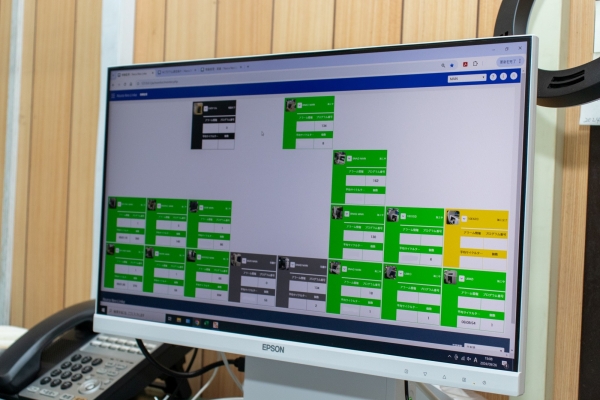
現在は、事務所のパソコンで機械の稼働監視と稼働管理を行い、モニター上に稼働状況を常時映しています。NCプログラムもパソコン上で一括管理するようになりました。
事務所と現場を往復して行っていたNCプログラムの送受信は、機械の前で完結できるように。1加工あたり10~15分かかっていた時間が、当初の予測どおりゼロになっています。
以前は、パソコンが壊れ、NCプログラムがすべて消えてしまうリスクがありましたが、DNCの導入とともにバックアップも万全となりました。無人運転中の稼働状況もスマホ上で確認できるため、加工に問題がなければ現場に来る必要もありません。
さまざまな不安が解消された今、「昔とは安心感がまったく違う」とのことです。
新明和ソフトテクノロジに依頼した結果について、鈴木さまは次のように語ります。
「導入前からアフターフォローまで、細やかに対応してくれるので助かっています。システム上、アップデートの難しいこともあると思いますが、山本さんは『お客さまの声があると、会社に対応を促しやすい』と、親身になって意見を聞いてくれるのがうれしいですね。
最近、相談しているのは、『転送したNCプログラムの表示について』です。弊社では『機械の型番+お客様名+品番』でプログラム名を管理しているのですが、機械の画面上には『機械の型番』しか表示されません。
同じ機種で同時に加工していると、正しい加工ができているか分かりません。これまでに加工間違いはありませんが、後輩が入ったこともあり、今後の改善に期待しています」と工場の今後を考えていることが伺えます。
また、次のステップに向けた前向きな意見も出ているようです。
「管理者側としては、工場全体の生産状況が見える化できたこともよかったです。弊社の受注品は、加工時間が数分/1個のものがほとんどです。1プログラムあたり、送受信時間が10~15分が短縮されたので、少なくとも日に10個以上は出来高が増えているはずです。
また(加工指示を出すのが勤務日なので)20日×15分として、月に5時間は余力が生まれています。この余力を生かし、難しい材料での形状など、特殊な加工や難しい加工を増やしていきたいですね。
やはり技術者としては、自社にしかできない加工にチャレンジできることがやりがいです。」
現場の困りごとからIoTの導入を検討し、これをよいきっかけにほかの課題も解決したコスズ製作所。生産余力が生まれ、技能者のモチベーションも高まる好例となりました。