Nazca Neo Linka 導入事例 CASE04
製造DXを叶えたい!
機械から取得する数字で、経営改善へ
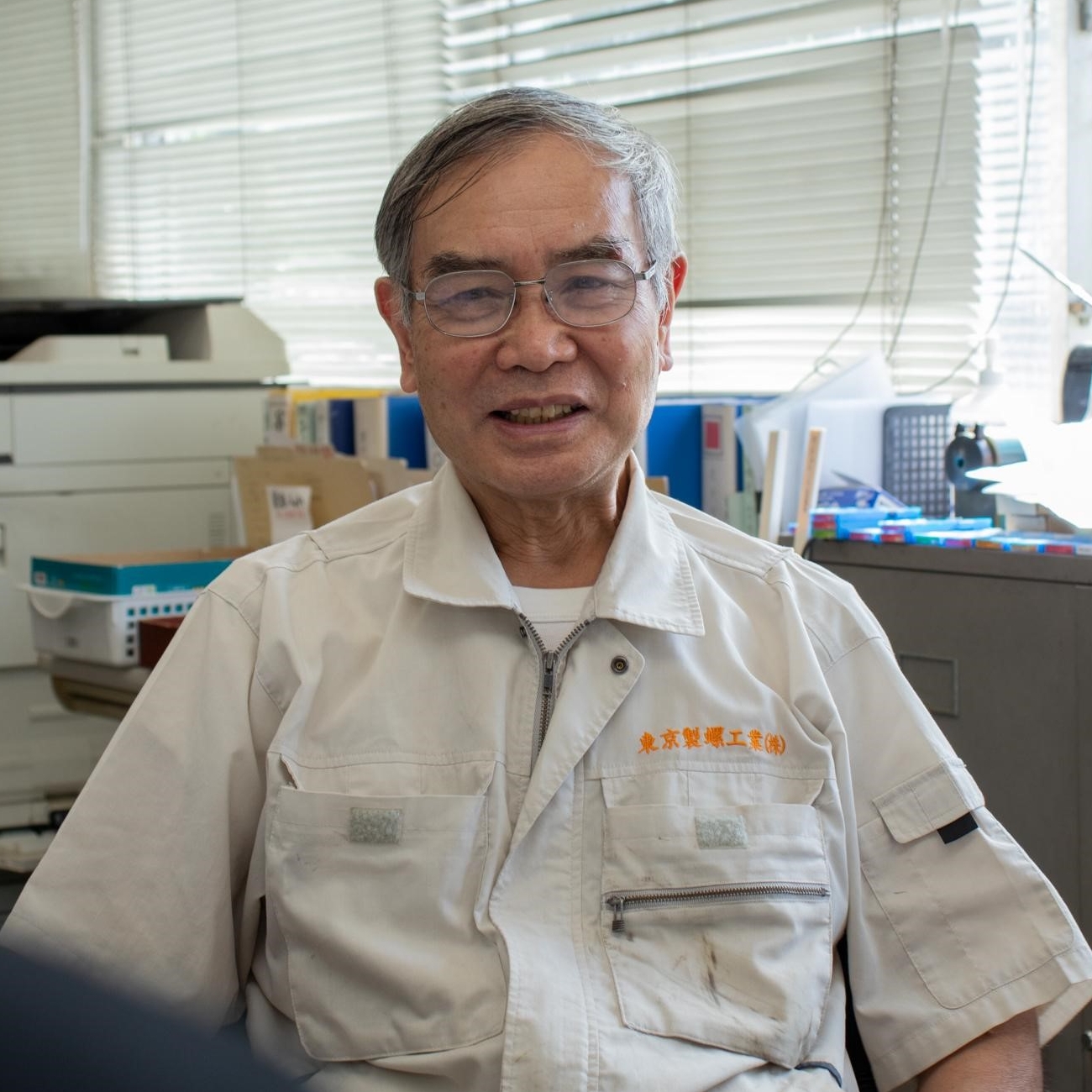
代表取締役 樋口 恵 氏
約3万個といわれる自動車部品。その中でも欠かせない部品の1つが、ネジです。汎用品だけでなく、車体の振動や熱に耐えうる強靭な特注品まで、1台あたり3,000個ものネジが使われています。
そんな自動車向けネジの製作を手がける老舗メーカーが、東京製螺工業株式会社(読み方:とうきょうせいらこうぎょう、以下:東京製螺工業)です。
東京製螺工業の創業は1935年。日本における自動車生産の黎明期から今まで、自動車産業の発展を縁の下で支えてきました。現在は、量産品と多品種少量品の両方を手がけ、500種類以上のネジを製造しています。
2代目として会社の発展に尽力してきた代表取締役の樋口恵さまは、DXの先駆けともいえる取り組みを進めてきました。
「工場全体の生産性を把握し改善につなげるため、2012年に基幹システムを自前で作ることにしました。将来的には、ITを活用した生産の見える化を実現したいと考えていました。」
基幹システムで、案件ごとに発行した指示書にバーコードを付与し、生産工程の開始から終了まで工程を管理しています。案件には、加工機や材料・工具などが割り当てられ、トレーサビリティを保証。ガントチャートによる進捗管理や納期管理が可能で、工場全体の生産性に寄与しています。
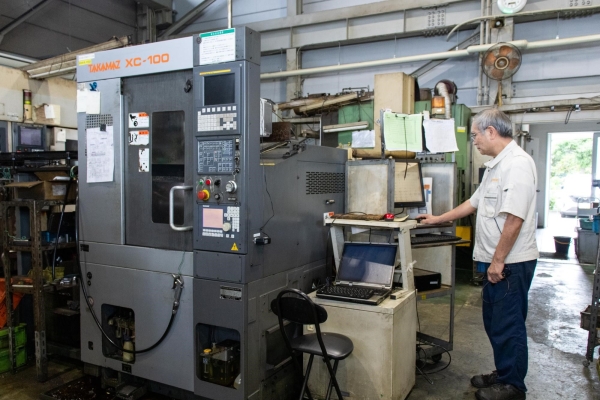
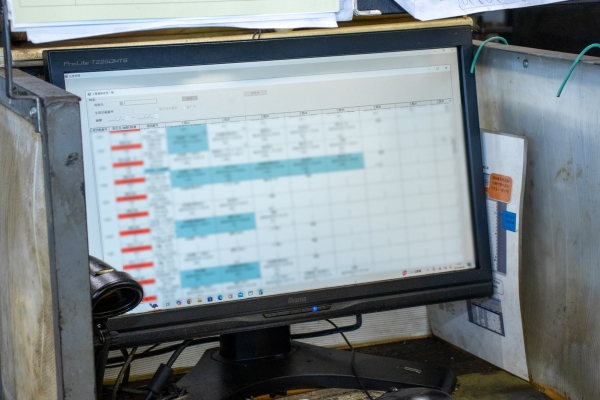
現場のパソコンで、案件ごとかつ工程ごとに進捗(水色=完了)を確認できる。
ただし、経営を効率化するうえで、必要な情報がいくつか取得できずに悩んでいた、と樋口さま。
「まず、生産進捗をタイムリーに把握できないことが問題でした。1日の生産個数や不良品数などは、担当者が日報に記載しないと数字を把握できなかったからです。また、機械の稼働状況を把握する仕組みもありませんでした。たとえば緊急停止があった際は、担当者が気付くまで停止が続いてしまうこともありました」
また、出来高の「結果」だけではなく、生産進捗の「経緯」もタイムリーに見られることが重要でした。その理由は、現場レベルの改善をうながす社風を作りたかったからです。
「社員数は10名ほどですから、担当者1人1人の自律性を応援することが大切です。担当者自身で予実を照らし合わせ、現場の状況に合わせて生産を調整できるようにしたいと考えていました。 そのために必要なデータは、会社から渡せるようにしたい。機械から直接稼働データを取れる仕組みを作れないか、と考えました。」
諦めかけていた製造DX、
ITを活用した工場の見える化を実現できたきっかけとは
東京製螺工業で、IoTシステムの導入検討が始まったのは、基幹システムを構想した2012年です。当時、CAD/CAM製品で付き合いのあったゴードーソリューション(新明和ソフトテクノロジの子会社)に相談をいただきました。ただ、当時は無線対応ができず、構想を断念していました。
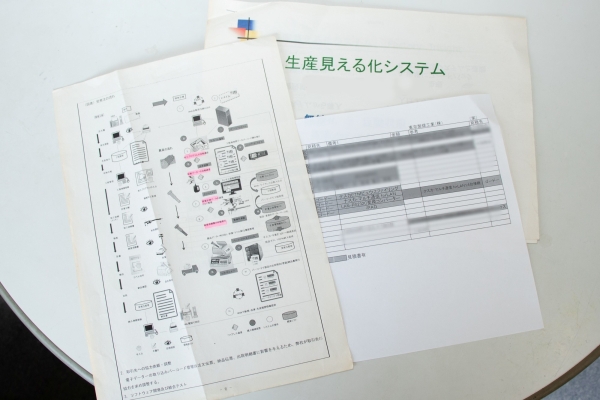
基幹システムを含むシステム構成や要件定義は代表が行った。
「弊社で受注する製品は流動的なため、製造する製品により機械や工具の配置替えがあります。よって、有線LANを引くことが難しいのです。
他社の無線端末機を使って、機械の稼働データを基幹システムに転送する仕組みも考案しました。しかしその方法も、試作機どまりで挫折してしまいましたね。」と樋口さま。
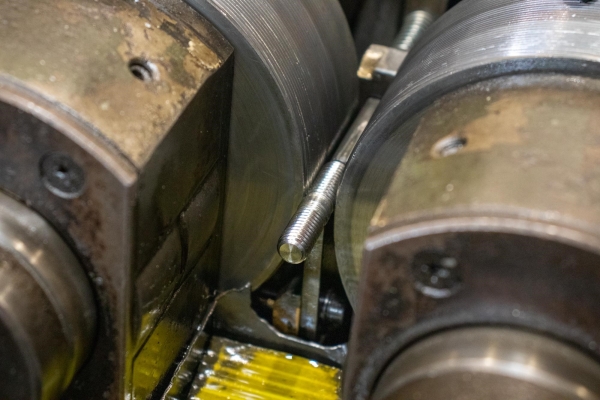
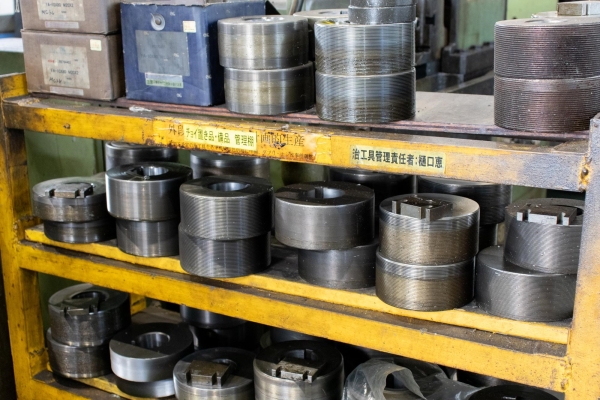
汎用的なネジは汎用機でネジ部を成形している。ネジの太さ、長さ、形状ごとに治具(専用の工具)が必要。
諦めかけていたころ東京製螺工業を訪問したのが、新明和ソフトテクノロジ ソリューション部 営業2グループ の山本優斗(以下、山本)でした。
「山本さんが私の悩みを丁寧に聞いてくれ、『IoTによる工場の見える化システムNazca Neo Linka(ナスカ・ネオ・リンカ、以下:Linka)なら、無線で生産進捗が把握できますよ』と教えてくれました。基幹システムとLinkaも連携できるとのこと。
とはいえ小さくない投資です。山本さんに相談すると、IT導入補助金の利用や、デモ機によるテスト運用などを提案してくれました。そうした細かな対応が、導入の決め手になりましたね。」
こうして、NC旋盤を中心に、7台すべての工作機械をLinkaに接続することが決まりました。
モノづくりの本質は「人」に尽きる、
IoTを活用して会社は社員のやりがいを高める環境づくりを
Linka導入後の工場の風景は一変しました。大型モニターには機械の稼働状況が映し出され、担当者が生産進捗を適宜確認しています。チョコ停(製造ラインの生産設備で一時的に停止や空転が発生する現象、小故障)が発生した時も、即座に気づけるようになり、ダウンタイムが大幅に減りました。
稼働中、非常停止、電源オフ、待機中の4つのステータスを色別に表示
また、経営を効率化するうえで必要だったデータの自動取得にも成功。生産実績やサイクルタイムなどの正確な数字が、NC旋盤から基幹システムに直接転送されています。
「生産余力を正確に把握できるようになりました。これにより、計画の細かな調整がスムーズになり、生産管理を実現しています。」と、樋口さまは満足げな表情を見せてくださいます。
Linkaの導入による一番の効果は何だったでしょうか?
「当初思い描いていたように、担当者の意識が高まりました。生産数や進捗率がリアルタイムに見えるので、皆さん自然とがんばってくれるんです。1人1人の工賃(直接加工時間:工賃=生産個数×単価)を計算し、全社で共有していることも大きいと思います。
つまり工賃は、担当者個人の出来高(売上げ)であり、弊社では給与に反映しています。
たまにエラーで正確なデータを取得できていないときは、担当者が『この数字、直してください!もっと作ってますよ』と教えてくれます。そうした声が挙がるのも、モチベーションが上がった証拠。皆さんががんばってくれた結果を見られるのは、うれしいことです。」
現場の自律性が増したことで、出来高も数パーセントずつ向上しているとのこと。 もともと残業はほぼゼロだという東京製螺工業。担当者の稼働時間を増やすことなく、生産性アップに成功しています。
また、そのほかの機能にも満足いただいている様子です。
「夜間の稼働状況も分かるようになったのは便利ですね。機械が停止してしまったときは、発生時刻や復旧までの時間がデータで残るのがよいです。
生産が集中している機械とそうでない機械が、一目瞭然になりました。案件の割り当てを調整し、工場全体の生産余力を確保しています」と樋口さま。
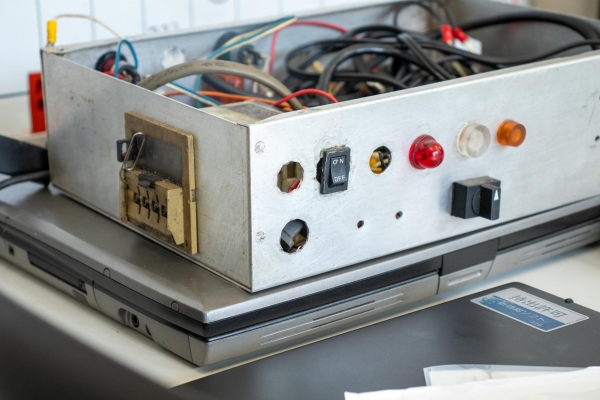
無線端末の試作機。分解・組み立てを繰り返した結果「通信の仕組みが分かり、今に生きている」とのこと。学びにムダはない。
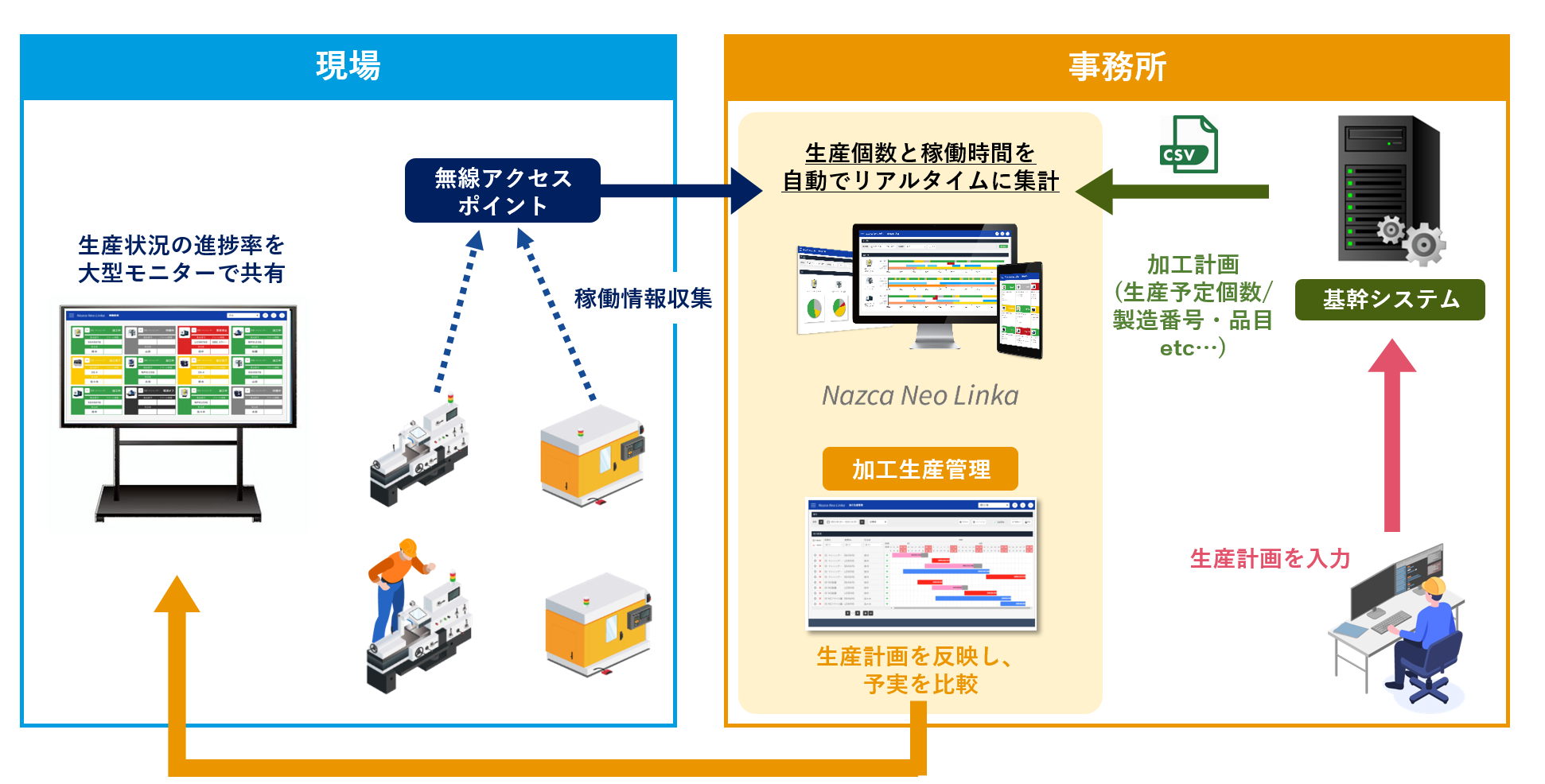
Nazca Neo Linkaと基幹システムの連携イメージ
一度はあきらめかけたDX。ですが、土台が整ってきたことで「まだまだやりたいことはたくさんある」と樋口さまの意欲も高まっています。
「モノづくりは結局のところ『人』に尽きます。私の理念としても、データの分析結果を現場の皆さんに渡し、仕事がもっと楽しくなる環境を作っていきたい。今後はデータ分析を進めたいと思っています。
新明和ソフトテクノロジさんにお願いしてよかったのは、山本さんと相談しながら構想を実現してこれたこと。やればできるという自信がつきました。
基幹システムを介した作業の自動化・効率化においても、加工プログラムの自動送受信や検査成績表の自動発行など、進めたいことがたくさんあります。今後も新明和ソフトテクノロジさんに関わっていただきながら、希望を実現していきたいです。」
経営者視点で数字の改善に取り組むことはもちろん、現場の「人」の力を信じる姿勢がとても勉強になります。経営者の飽くなき探求心が、真のDXにつながりつつある好例でした。