Nazca Neo Linka 導入事例 CASE03
工場の見える化で抽出されるデータを活用し、
機械ごとに生産進捗率を把握するシステムを構築
大正時代に鍛冶屋として創業した田村技研工業株式会社。時代の流れに合わせて業態を変化させ、現在は半導体製造装置をはじめ医療機器や産業用設備などに用いられる多品種少量の精密部品を手掛けています。
単一の製品をたくさん作る大量生産と異なり、1日に何種類もの部品を製造する多品種少量生産の業態は、段取り替えの頻度が高くなるため、機械を止めている時間が長くなりやすいのが悩みです。
「多品種少量生産において利益率を高めるには、機械ごとの稼働時間を詳細に把握し、それぞれの稼働率を少しでも高めていく努力が必要です。これまでも日報で稼働率の把握に努めてきました。しかしながら、手書きによる集計は時間がかかりますし、機械操作のかたわらで記載するため、書きそびれてしまう時間帯もありました」と、代表取締役社長の田村昌樹さま。
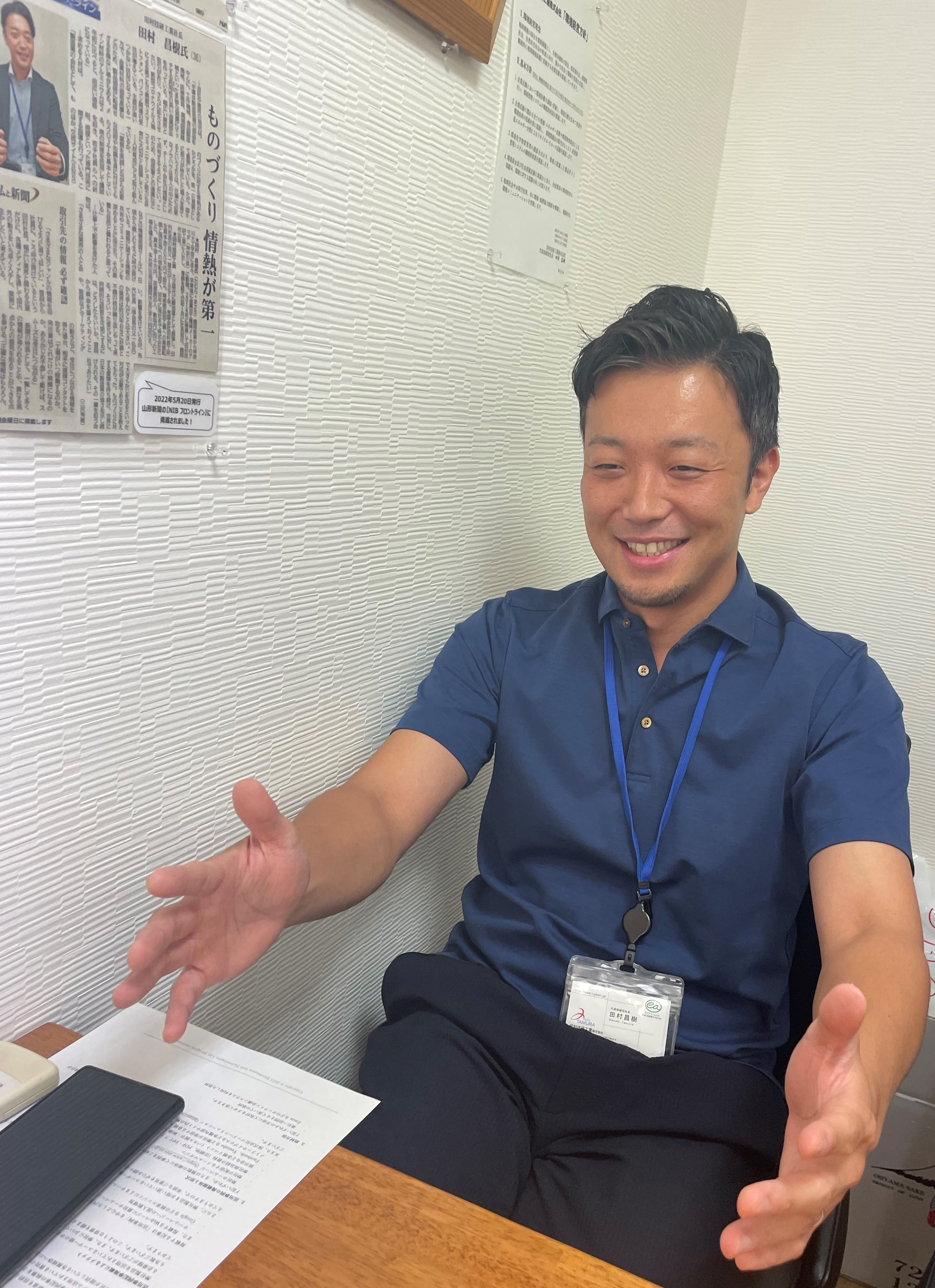
代表取締役社長 田村 昌樹 氏
「そうした背景から、機械の稼働状況を把握するシステムの必要性を感じていました。さらに、機械あたりの生産進捗率をリアルタイムに把握できるシステムを導入したい、と思うようになりました」と続けます。
機械の稼働状況をデータ集計しながら、生産計画に対する現在の進捗率をリアルタイムに見られるシステムを導入するという構想は描けたものの、どの会社に依頼すれば実現できるか分からなかったといいます。そこで、かねてから付き合いのあった商社さまにご相談されました。
「いただいた候補のなかに、新明和ソフトテクノロジさんの名前がありました。実は、以前から、NCプログラムの送受信ソフト『NAZCA5 DNC(ナスカ・ディーエヌシー、以下:DNC)』を使っており、『その制作会社で工場の稼働管理システムも作っていますよ』と紹介を受けたのです。
DNCへの信頼感があったので、商談を設定してもらいました。すると、私の構想に対して『新明和ソフトテクノロジでも、いただいた構想は初めてのカスタマイズになりますが、ぜひ実現しましょう!』と、よい返答をいただいたのです」
このようにして2021年の5月より両社の共創が始まりました。主要な工作機械20台をNazca Neo Linka(ナスカ ネオ リンカ、以下:Linka)に接続し、生産進捗率をリアルタイムに反映するようなカスタマイズを実施することになりました。
細かな仕掛けが社員の意識付けとなり行動変容を促す
大きな課題は、進捗率をリアルタイムに演算処理するプログラムをどのように構築するかでした。窓口を担当した新明和ソフトテクノロジ 東日本営業グループ営業ユニットリーダーの山本優斗は、次のように語ります。
「Linkaは機械の稼働データを吸い上げ、稼働率を計算します。そのシステムにデータベースを追加し、生産計画の数値を目標値として入力できるようにしました。そして、機械の稼働時間の実績数値と生産計画の数値を即時に演算処理するプログラムを構築し、1日の生産計画に対する進捗率が毎秒計算されるようなシステムを構想しました」
さらに工夫したのは、機械が稼働していない時間帯の項目も細分化したことです。「段取り中」や「待機中」はもちろんのこと、「不良品加工」などの項目も設けました。これにより、機械が止まっている原因を社員のみなさんが一目で把握できるようにしたのです。
本件は、新明和ソフトテクノロジでも初めてのカスタマイズ内容となりました。それでも取り組みに対する全社的な合意を得られたのは、多品種少量生産の業態のお客さまから、同様のカスタマイズについてご要望をいただくことが増えてきたためです。
山本自身も、「大量生産の業態においては、Linkaの導入で工場の稼働率が向上した実例が増えてきました。そんななか、多品種少量生産のお客さまにもお役に立ちたい気持ちが芽生えていったのです」と想いを語りました。
現在、田村技研工業の生産現場には5台のモニターが設置され、オペレーターの社員さまが作業をしながらいつでも稼働率を見られるようになっています。
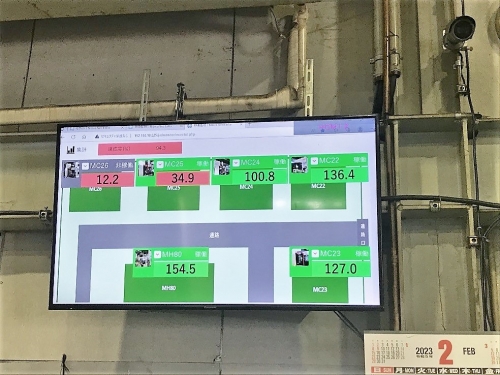
工場内モニターイメージ図
機械別の稼働状態がパーセンテージで表され、画面の左上にはエリア平均の達成率が表示されている
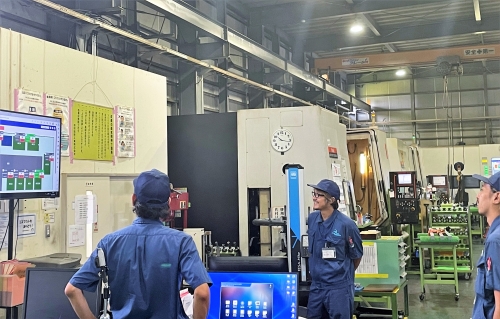
生産現場内 Linka運用イメージ図
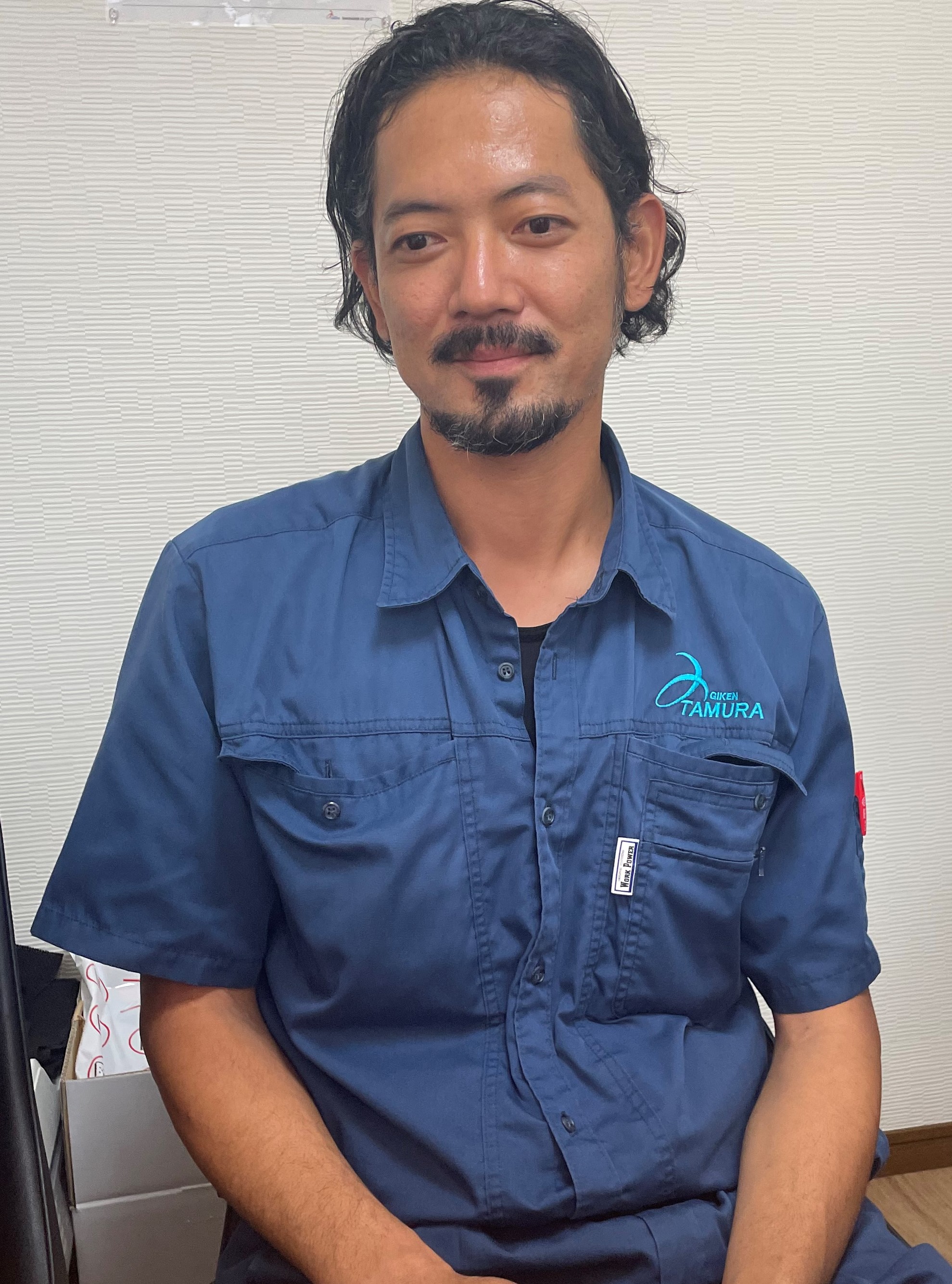
オペレートリーダー 工藤 博貴 氏
そして、導入から半年が経ち、現場にはよい変化が見られているようです。オペレートリーダーの工藤博貴さまは、次のようにご自身の変化を教えてくださいます。
「作業中に現在の稼働率がパッと目に入るので、状況に応じて各オペレーターの行動が変わるきっかけになりました。とくに生産目標から遅れているときは、遅れを取り戻すべく、スピードアップして対応しています」
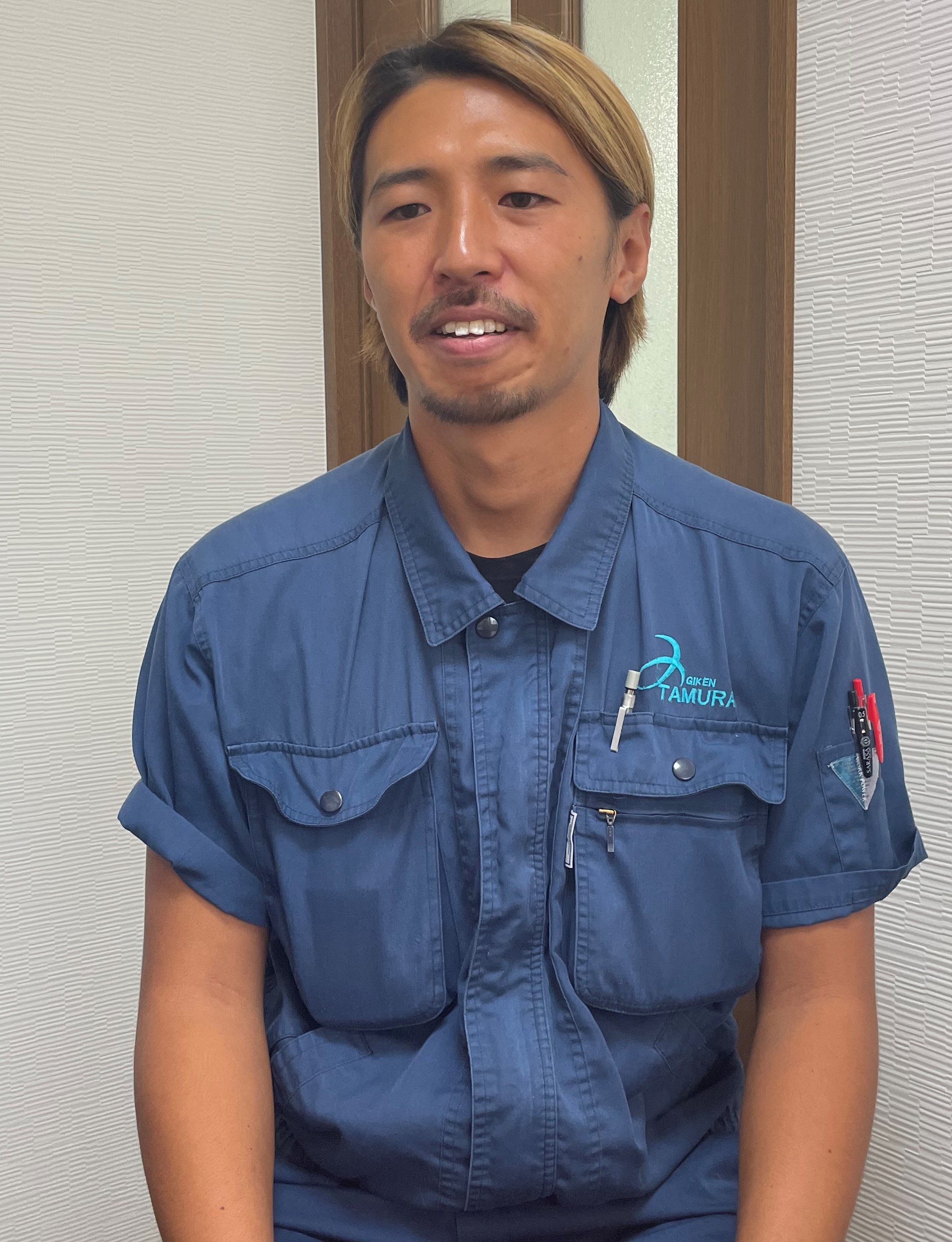
オペレートリーダー 石川 裕太 氏
同じくオペレートリーダーを務める石川裕太さまは、「時間を横軸とした棒グラフで稼働状況が見えるので、『朝の段取りに時間を使いすぎてしまったな』など、その日のオペレートの段取りを振り返るようになりました。機械が稼働していない原因を分析する習慣ができたのは、大きな変化です」
製造部長の高橋淳さまは、稼働率の変化にも気づいている様子です。
「とくに放電加工機の稼働率が大幅に向上しています。電流の作用によってコンマ数ミリ単位の超微細な加工を行う放電加工の作業は、仕上げなどの後工程に回しがちです。そのため、放電加工機の稼働状況にはバラツキがありました。
今は、オペレーターが機械の空き状況を見ながら、後工程に予定していた製品の放電加工を先に持ってくるなど、独自に判断・調整しています。放電加工機を持て余している時間が減りました」
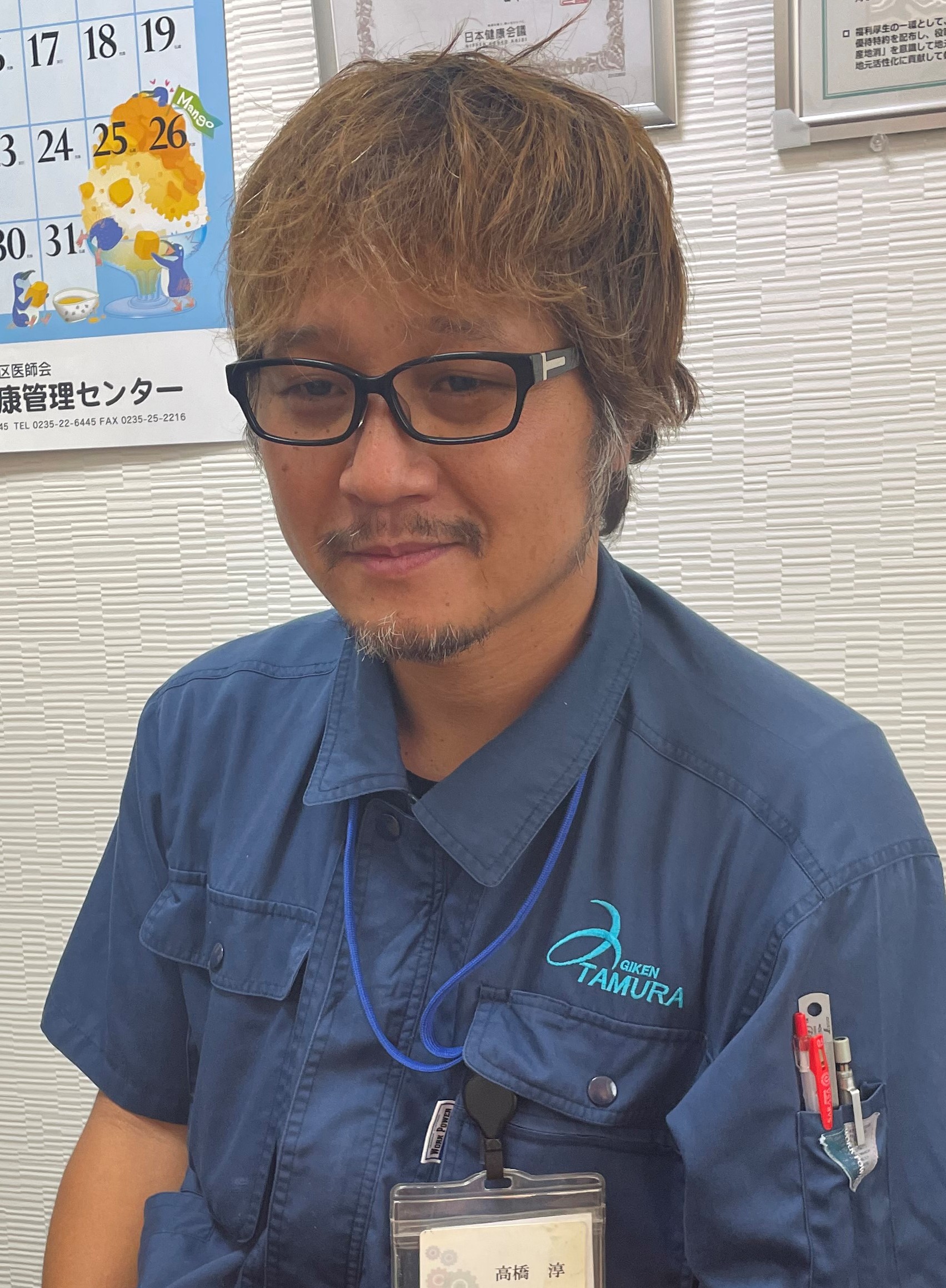
製造部長 高橋 淳 氏
高橋さまのコメントを受け、田村さまも次のように意気込みを語ってくださいました。
「今はLinkaを使って分析に必要なデータを蓄積している段階で、本格的な改善は次のフェーズだと考えています。それでも、手書きで稼働率を集計していた時間が1日あたり30分から1時間削減することができましたし、稼働率が可視化されて現場の士気も高まりました。
弊社では、社員の勤務時間のうち、50パーセント以上を機械の稼働時間に充てることを目標としています。その目標に向け現場が一丸となるベースが作れました」。
工場のボトルネックが見つかり、次のフェーズでは定量の改善に挑戦
大がかりなカスタマイズとなった今回。どのような基準でこのシステム投資を決めたのか、田村さまは次のように語ります。
「稼働管理システムが直接的に利益を生むのではないことは、多くの経営者が思うところかもしれません。しかし、利益という定量を改善するには、定性を変容することが重要だと考えます。
実は、以前に社員が手書きで集計していた稼働率と、Linkaが集計する稼働率には、大きな差がありませんでした。それはつまり、社員が誠実にモノづくりに取り組んでいることの裏返しです。弊社では社員育成に力を入れ、目標を定量化し数字で考える文化も醸成してきました。
そうした前提の上に、それぞれの社員が生産進捗率を把握できる仕組みを導入することで、社員のモチベーションが高まり(=定性の変容)、行動が変わり、定量が改善されていくと考えています」。
Linkaの導入から半年が経ち、今では工場内のボトルネックも把握できつつあるようです。最後に、今後の展望について田村さまに聞きました。
「ボトルネックがわかっても、改善方法は人が考え実施しなければいけません。その作業は機械やAIに置き換えられないからこそ、多品種少量生産の業種で稼働率を向上するのは一筋縄にいかないと痛感します。
ときには成功パターンを勉強することも必要です。山本さんに相談したところ、新潟県柏崎市の有限会社藤巻製作所さまを紹介してくれ、見学できるよう段取りしてくださいました。こうした製造業のお客さまネットワークを持っているのも、新明和ソフトテクノロジさんの強み。今後も弊社のITパートナーとして、弊社の生産性向上をご支援いただけたらと思います」。
多品種少量生産の現場で稼働率向上を目指す画期的な取り組み事例となりました。
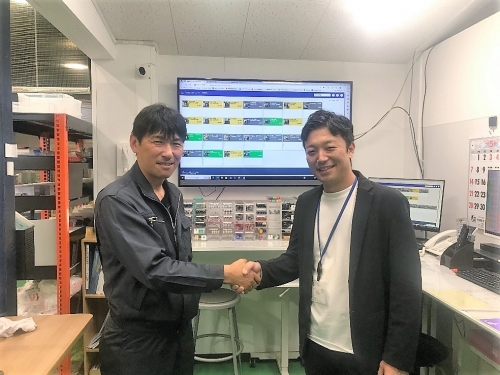
(左から)藤巻製作所 代表取締役 藤巻 健 氏、田村技研工業株式会社 代表取締役社長 田村 昌樹 氏